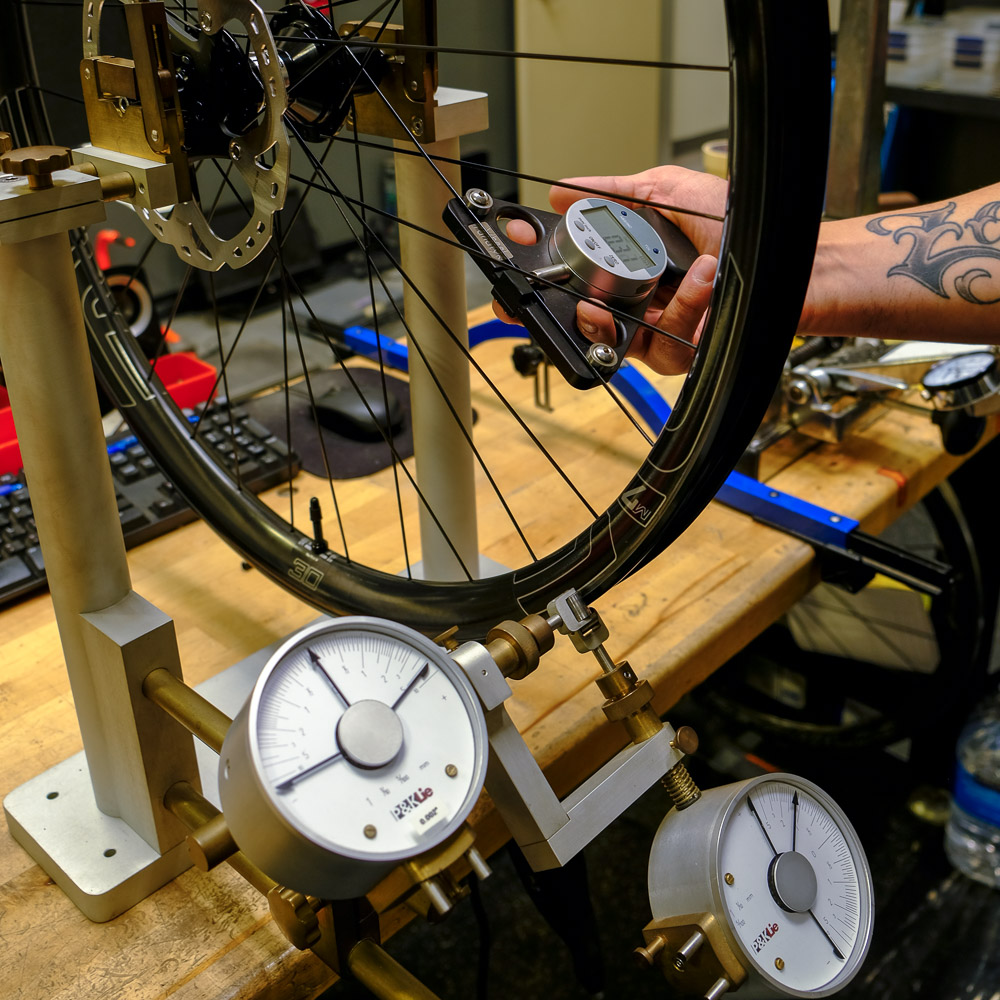
Spokes General Principles
Modern spokes are available in a variety of lengths, shapes, materials, finishes, and attachment types. All spokes provide the basic function of connecting the hub to the rim. This seemingly straightforward static function becomes far more complex when we consider dynamic loading patterns. Bicycle wheels operate under complex repeated loading conditions referred to as "fatigue cycles". Spokes must carry combined loading from the following primary sources.
- Wheel tension: Stress caused by tightening spokes during a build. Tension can be as high 100-130 Kg per spoke.
- Rider weight: Heavier mass increases stress under cyclic fatigue loads.
- Torque loading: Rear wheel power input as well as disc brake forces add torque to the entire spoke system.
- Tire pressure: Increased tire pressure has the effect of causing lower spoke tension, which increases fatigue sensitivity.
- Impact loading: Potholes or trail features cause large tension fluctuations in a spoke system.
- Lateral loading: Stress caused by side loading of a wheel.
Spokes behave similar to bolts by stretching under tension and using the energy held in the material to resists complex dynamic loads. Spoke tension cannot be determined by visually inspecting a wheel and is independent of wheel straightness. Evaluation of maximum tension and uniformity can be measured with a tensiometer, and is critical to long-term fatigue life of a wheel system.
While it is not practical to calculate fatigue life cycles for every custom wheel, there are a few key considerations you can make when selecting spokes.
- Heavy riders or heavy duty applications: consider heavier gauge spokes with thicker cross sections for increased lateral stability.
- Heavy riders or heavy duty applications: use higher spoke counts to lower individual spoke stress over millions of fatigue cycles. This can dramatically improve long term durability.
- Use bladed spokes to reduce weight and control high tension wind-up for high performance applications.
- Bladed spokes will contribute to slightly lower lateral stiffness due to less cross sectional area in the lateral plane.
- Always use a slightly longer rather than a slightly shorter spoke to protect against failures of the spoke thread and nipple.

Aerodynamic Bladed Spokes
These spokes are useful for road, triathlon, time trial, cross-country or other applications where the reduction of aerodynamic drag is crucial to maximum performance. Aerodynamic spokes can be identified by their ovalized or bladed cross sections.
An added benefit to building with bladed spokes is the ability to control wind-up at higher tension. Bladed spokes can be stabilized using a bladed tool holder to help control twisting and tension uniformity with much greater precision. Round spokes will twist at higher tension and twisting can be difficult to control on narrower wire.

Double Butted Round Spokes
Can be easily identified by a change in spoke wire diameter near the head of the spoke and near the threaded portion of the spoke. Double butted spokes are lighter than straight gauge and offer better ride qualities due to a more flexible center section. Double butted spokes are generally very strong, however spokes with 1.5mm center sections can be challenging to build at higher tension due to twisting. Ultra thin center sections are not recommended for disc brake applications.

Single Butted Spokes
These spokes can be identified by a single change in diameter between the neck and the body of the spoke. The neck is slightly thicker than the body to improve durability for disc brake and other heavy-duty applications. Single butted spokes are slightly heavier than double butted, but offer incremental lateral stiffness gains. Single butted spokes are popular for high torque or E-bike applications where extra material at the neck can be beneficial to durability. Single butted spokes with 2.3mm neck diameters are also useful for wheels to be rebuilt with used hubs that have worn or oversized mounting holes in the flanges.

Straight Gauge Spokes
These can be identified by a constant wire diameter throughout their length, which makes them slightly heavier than double butted spokes. Straight gauge spokes offer higher lateral stiffness compared to bladed or Double Butted due to their thicker cross section. These are the simplest spoke type and can be used for general purpose or heavy-duty applications. One benefit to both straight gauge and single butted spokes is their ability to be custom cut into ultra short lengths due to a constant wire diameter.